Understanding Concrete Mixing Plants: Essential Components and Benefits
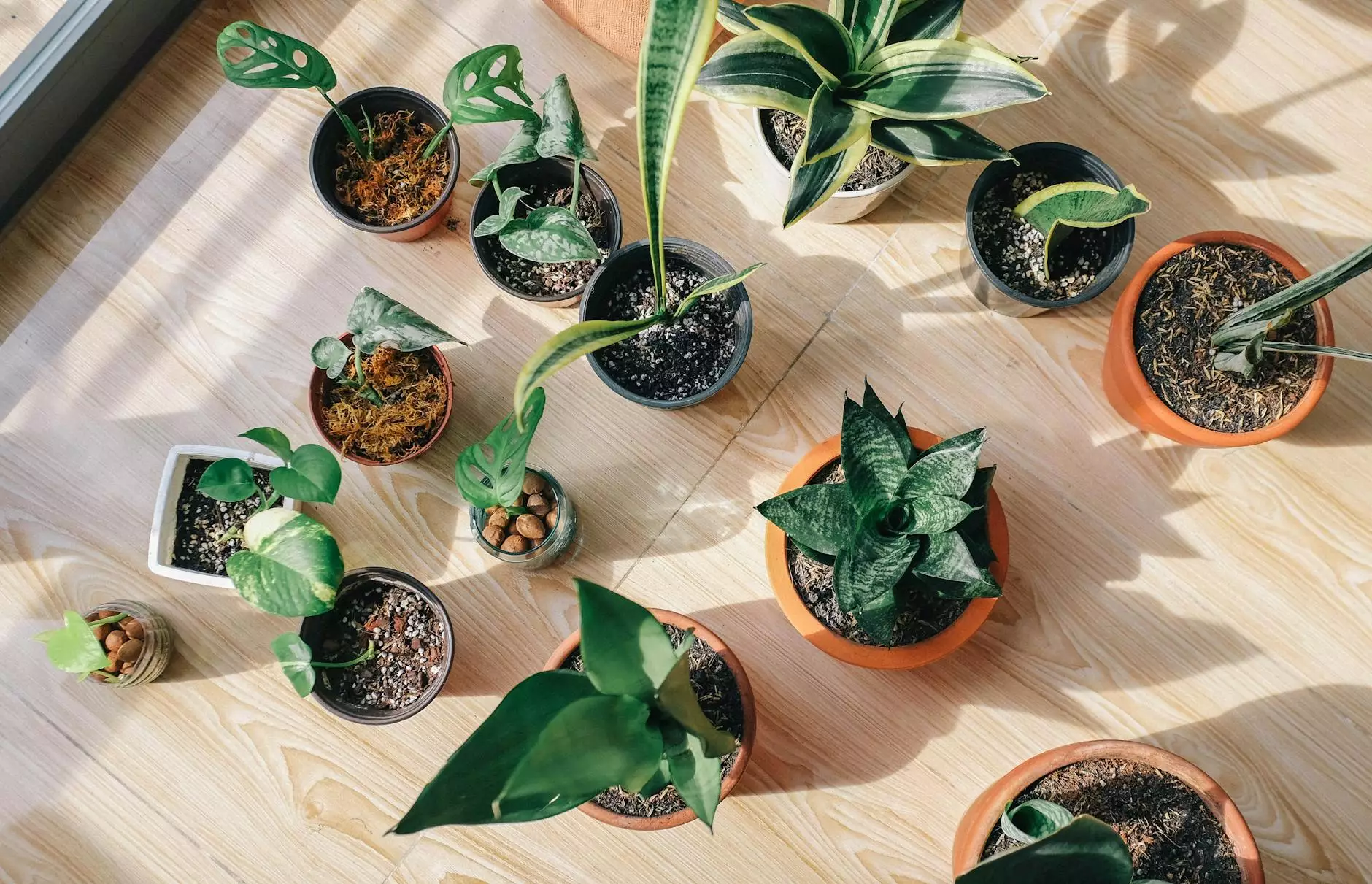
In the ever-evolving realm of construction, concrete mixing plants play a pivotal role, serving as the backbone for creating high-quality concrete that meets the rigorous demands of modern infrastructure projects. This article delves deep into the world of concrete mixing plants, exploring their components, types, importance, and cutting-edge technology that defines this critical aspect of the construction industry.
The Importance of Concrete Mixing Plants in Construction
Concrete is often referred to as the most widely used man-made material on the planet. A concrete mixing plant is where various raw materials are combined to produce concrete. The importance of these plants cannot be overstated; they ensure the consistency, strength, durability, and workability of concrete required for different construction projects.
Key Benefits of Using Concrete Mixing Plants
- Quality Control: Mixing plants offer precise control over the material proportions, ensuring that the concrete meets necessary quality standards.
- Efficiency: Automated mixing processes speed up production, reducing wait times and improving overall project timelines.
- Customization: Concrete can be tailored for various applications, from residential buildings to large-scale infrastructure projects.
- Environmental Considerations: Modern mixing plants often incorporate recycling systems and energy-efficient technologies, mitigating the environmental impact of concrete production.
- Reduced Labor Costs: Automation decreases the dependency on manual labor, leading to significant cost savings in labor-intensive tasks.
Components of a Concrete Mixing Plant
A typical concrete mixing plant comprises several key components, each playing an essential role in the production process. Understanding these components helps appreciate the sophistication and functionality of modern mixing plants.
1. Aggregate Bins
Aggregate bins store various sizes of aggregates such as sand, gravel, and crushed stone. They ensure the necessary material is available for mixing, and their design often includes weighing systems to maintain accuracy.
2. Weighing System
This system ensures precise measurement of each ingredient, including aggregates, cement, water, and additives. Accuracy is crucial for producing high-quality concrete.
3. Mixer
The heart of the concrete mixing plant is the mixer, where all ingredients are combined. There are several types of mixers, including:
- Batch Mixers: Produce concrete in batches and are ideal for small to medium projects.
- Continuous Mixers: Provide a continuous supply of concrete, efficient for large-scale projects.
4. Control System
A sophisticated control system allows operators to monitor and manage the mixing process. Many modern plants use computerized controls for optimal efficiency and easy monitoring.
5. Storage Silos
Storage silos are essential for bulk cement storage. They protect the cement from moisture and contamination, ensuring the quality of the final product.
6. Discharge System
This system transfers the mixed concrete to trucks or site-specific locations for use. Efficient discharge systems minimize waiting time and optimize workflow.
Types of Concrete Mixing Plants
Concrete mixing plants come in various types to cater to different project needs. Here are the main types:
1. Stationary Concrete Mixing Plants
These plants are permanently located and usually employed for large-scale construction projects like highways, bridges, and industrial buildings. Their design allows for high production volumes and precision.
2. Mobile Concrete Mixing Plants
Mobile plants are designed for portability, making them suitable for temporary projects. They can be easily relocated based on project demands, making them ideal for construction sites without permanent facilities.
3. Compact Concrete Mixing Plants
These are designed for medium to small-scale projects where space is limited. They integrate all components into a compact unit, simplifying installation and operation.
Innovative Technologies in Concrete Mixing Plants
With advancements in technology, concrete mixing plants have incorporated various innovative practices to enhance efficiency, sustainability, and productivity. Let’s explore some of these cutting-edge technologies:
1. Automation and Robotics
The introduction of automation in concrete mixing plants has revolutionized the industry. Automated systems reduce human error, increase production rates, and ensure consistent quality. Robotics can also be used for material handling, leading to further efficiency.
2. Smart Mixers
Smart mixers equipped with sensors and IoT capabilities can monitor mixing conditions in real-time, allowing for immediate adjustments to maintain optimal concrete quality.
3. Integration of Renewable Energy Sources
Many modern mixing plants are integrating renewable energy sources, such as solar panels, to power their operations, significantly reducing their carbon footprint and operational costs.
4. Recycling Systems
Innovative recycling systems can repurpose waste concrete and materials, contributing to sustainability in the construction industry. These systems allow leftover concrete to be processed and reused, minimizing environmental waste.
Challenges Faced by Concrete Mixing Plants
Despite their advantages, concrete mixing plants face several challenges that must be addressed to maintain efficiency and profitability:
1. Material Supply Chain Issues
Supply chain disruptions can impact the availability and cost of raw materials. Establishing reliable suppliers and contingency plans can mitigate these risks.
2. Regulatory Compliance
Concrete mixing plants must adhere to stringent environmental regulations regarding emissions and waste management. Investing in compliance technologies is crucial for sustainable operations.
3. Workforce Management
Finding skilled labor to operate advanced mixing plants can be challenging. Continuous training and development programs are necessary to equip workers with the needed skills.
Best Practices for Operating Concrete Mixing Plants
To ensure that a concrete mixing plant operates efficiently and sustainably, certain best practices should be implemented:
1. Regular Maintenance
Implementation of a regular maintenance schedule is crucial to prolong the lifespan of the equipment and ensure safety and efficiency.
2. Employee Training
Investing in employee training ensures workers are knowledgeable about safety protocols, equipment handling, and quality control measures.
3. Sustainability Practices
Adopting sustainability practices, like using recycled materials and minimizing waste, can enhance the plant’s reputation while also reducing operational costs.
4. Efficiency Audits
Conducting regular efficiency audits can help identify areas for improvement in the mixing process, ensuring optimal productivity and resource usage.
Conclusion: The Future of Concrete Mixing Plants
The future of concrete mixing plants looks promising with the advent of advanced technologies and sustainable practices. As the construction industry continues to grow, so will the demand for high-quality concrete produced efficiently. By embracing innovation, addressing challenges, and following best practices, concrete mixing plants can significantly contribute to building the infrastructure of tomorrow.
For businesses and stakeholders in construction, staying informed about the latest trends and technologies in concrete mixing plants is crucial for maintaining a competitive edge. Investing in high-quality mixing plants can lead to exceptional project outcomes, longer-lasting structures, and a reduced environmental impact.
To learn more about advanced concrete mixing plants and how they can optimize your construction projects, you can explore the offerings from polygonmach.com.