The Future of Construction: Embracing Prefabricated Containers
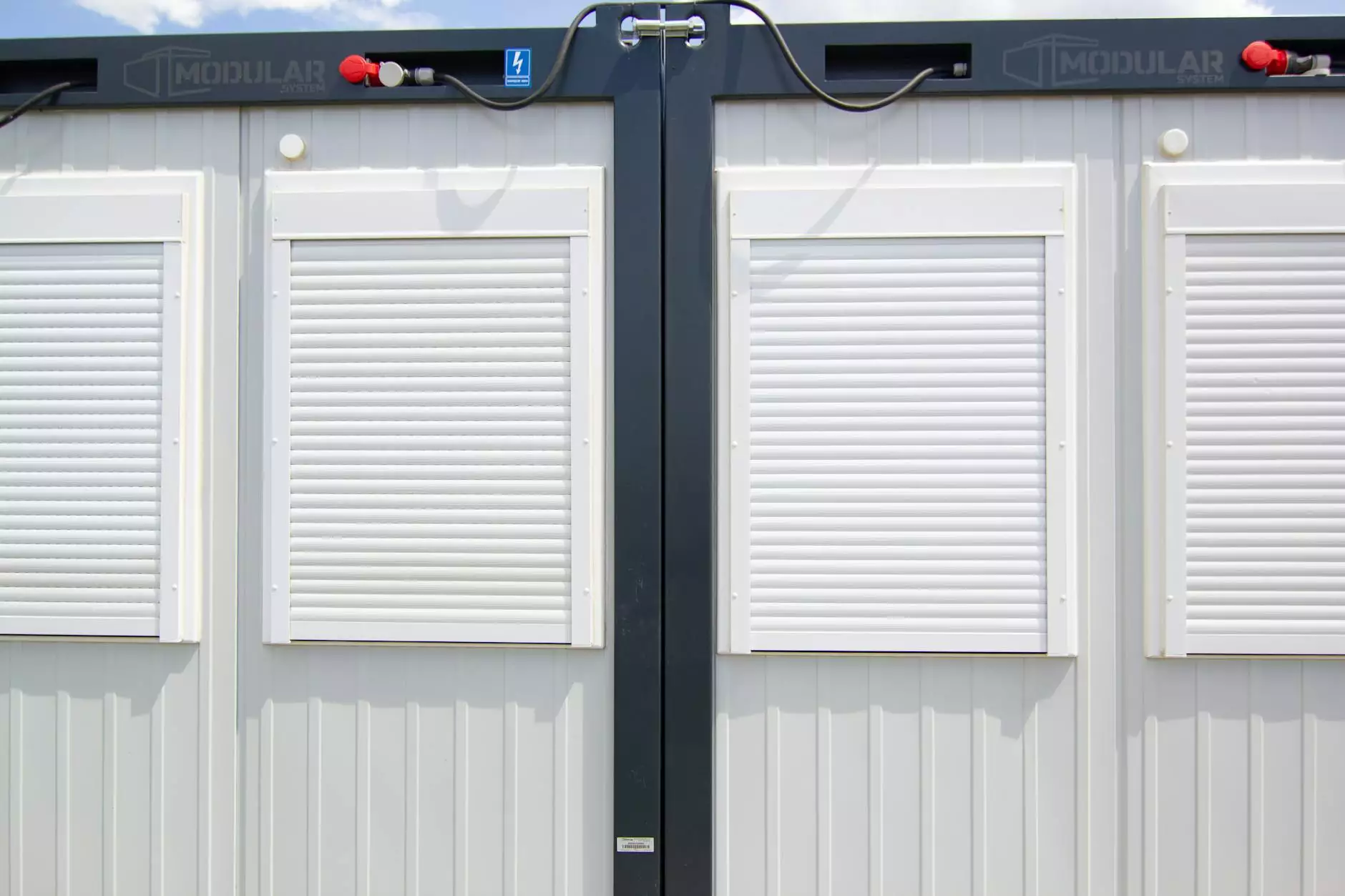
In an ever-evolving construction landscape, the demand for innovative solutions has never been greater. One such solution that has gained significant traction in recent years is the use of prefabricated containers. These versatile structures are revolutionizing the way contractors and developers approach building projects, providing a multitude of benefits that are hard to ignore.
What Are Prefabricated Containers?
Prefabricated containers are modular units created off-site, which can be rapidly assembled onsite. They are often made from shipping containers that have been adapted for various uses, from residential spaces to offices and even luxury accommodations. Their design allows for easy customization and flexibility, catering to a broad range of needs.
Why Choose Prefabricated Containers?
1. Speed of Construction
One of the most compelling advantages of prefabricated containers is the incredible speed at which projects can be completed. Traditional construction methods often involve lengthy timelines attributed to various factors, including permitting, weather, and labor availability. In contrast, prefabricated containers can be manufactured in a controlled environment, minimizing delays. Key benefits include:
- Reduced build times: Since much of the work is completed off-site, projects can see a significant drop in overall construction time.
- Faster occupancy: Rapid construction means that clients can move in sooner, generating income quicker.
2. Cost-Effectiveness
When considering the costs associated with construction, prefabricated containers present a financially savvy option. The reduction in onsite labor and the efficiency of the building process lead to lower overall costs. Factors contributing to this cost-effectiveness include:
- Reduced material waste: Prefabrication minimizes waste, allowing for more efficient use of materials.
- Lower labor costs: With the majority of the work done off-site, fewer labor hours are needed on-site, reducing payroll expenses.
3. Sustainability and Environmental Impact
As the world shifts toward more sustainable building practices, industries must adapt to meet these demands. Prefabricated containers offer a solution that aligns with eco-friendly initiatives. Benefits include:
- Recycling materials: Many prefabricated containers are modified shipping containers, promoting recycling and reducing waste.
- Energy efficiency: Modern prefab designs can include energy-efficient solutions, such as solar panels and green roofs, significantly reducing their environmental footprint.
Applications of Prefabricated Containers
The versatility of prefabricated containers makes them suitable for a wide array of applications across various industries. Here are some common uses:
1. Residential Homes
Many homeowners are opting for prefabricated containers as a cost-effective and unique housing solution. These homes can be customized to meet individual needs, offering a modern twist on traditional housing.
2. Commercial Office Spaces
Businesses are increasingly turning to prefabricated containers for office spaces, particularly in urban areas where space is at a premium. These modular offices can be easily transported and rearranged to fit growing company needs.
3. Pop-up Shops and Restaurants
The ability to set up temporary structures quickly makes prefabricated containers an excellent choice for pop-up shops and restaurants. They allow business owners to test markets without the long-term commitment of a traditional lease.
4. Disaster Relief and Emergency Housing
In the wake of natural disasters, prefabricated containers can be deployed quickly to provide emergency shelter, proving their worth in urgent situations.
Challenges and Considerations
While the advantages of prefabricated containers are compelling, it is essential to consider potential challenges:
1. Zoning and Regulations
Building regulations can vary significantly between locations, and it’s crucial to understand local zoning laws before committing to a prefabricated container project. Some areas may have restrictions on the use of containers for building.
2. Higher Initial Investment for Custom Designs
While overall costs can be lower, custom designs may require a higher initial investment. It’s important to weigh the long-term benefits against short-term costs.
Best Practices for Implementing Prefabricated Containers
To maximize the benefits of prefabricated containers, consider the following best practices:
1. Partner with Experienced Contractors
Select contractors who are experienced in working with prefabricated containers. Their expertise can ensure a smoother building process and compliance with local regulations.
2. Invest in Quality Materials
Prioritize quality materials and finishes for your prefabricated container project. This will not only improve aesthetics but also enhance durability.
3. Plan for Utilities and Infrastructure
Ensure that plans for plumbing, electrical systems, and HVAC are carefully designed before assembly. Incorporating these systems into the design phase can prevent complications later on.
Conclusion: The Future of Building with Prefabricated Containers
The construction industry is at a critical juncture, and embracing innovations like prefabricated containers can pave the way for a more efficient, sustainable, and cost-effective future. With their myriad advantages, it is easy to see why they are becoming a preferred choice for contractors and builders alike.
If you are considering a project and want to explore the potential of prefabricated containers, visit Module T for more insights and solutions tailored to your needs. Harness the power of modern technology in construction today!