Understanding the Importance of Automobile Plastic Mold in Modern Manufacturing
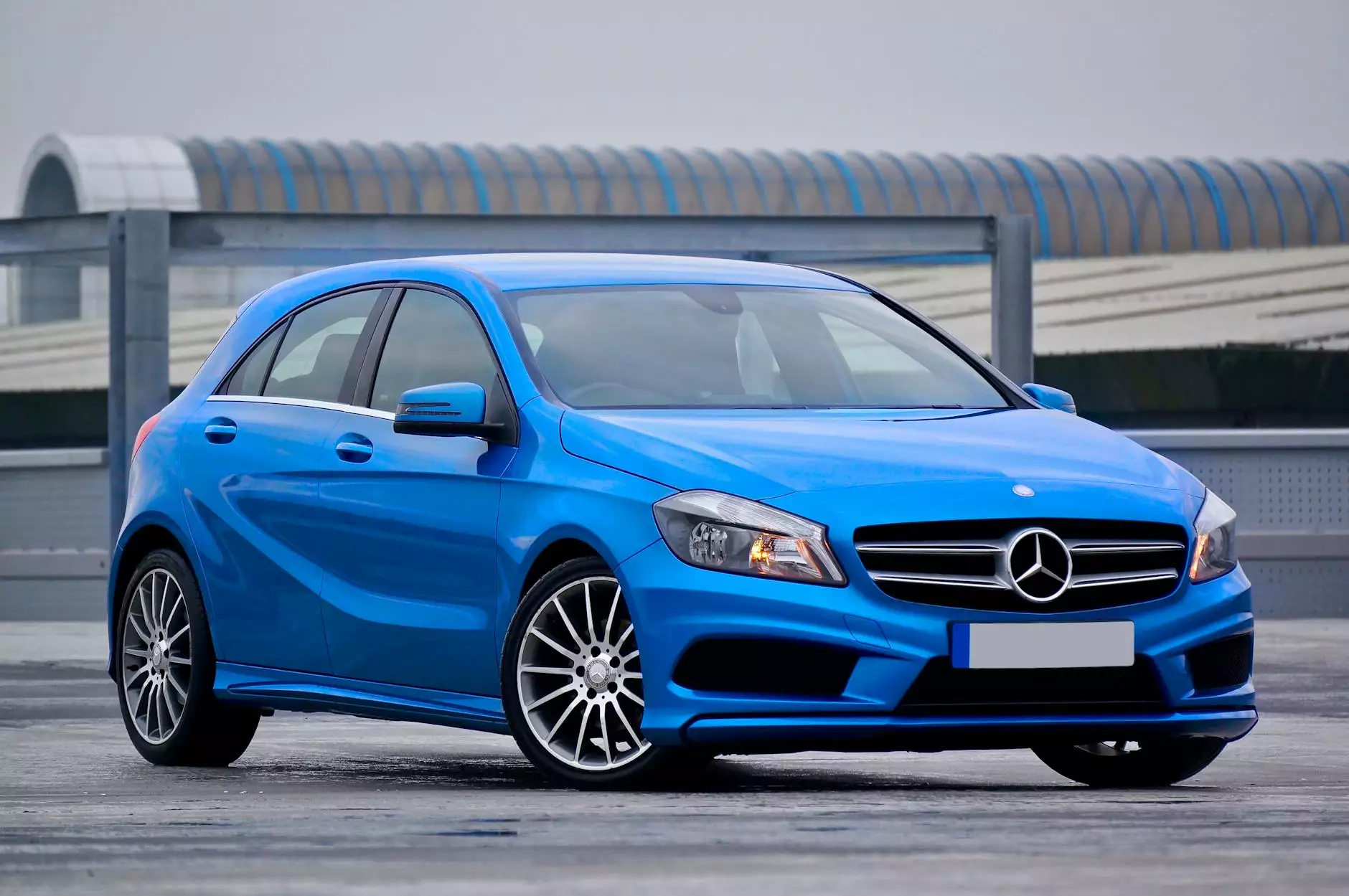
In today’s rapidly advancing industrial landscape, the role of automobile plastic mold technologies cannot be overstated. These sophisticated molds are at the heart of manufacturing processes that shape the future of the automotive industry. This article delves into the critical aspects of automobile plastic molds, encompassing their applications, benefits, and the future trends reshaping manufacturing paradigms.
The Evolution of Molding Techniques in the Automotive Industry
The automotive industry has witnessed significant transformations over the years, especially in molding techniques. Traditional metal molds have given way to innovative automobile plastic mold solutions that offer numerous advantages including weight reduction, cost efficiency, and design flexibility.
From Metal to Plastic: A Paradigm Shift
Initially, metal was the go-to material for manufacturing automotive parts. However, as technology progressed, manufacturers realized the potential benefits of using plastic, leading to a shift towards:
- Reduced Weight: Plastic components are lighter than their metal counterparts, contributing to enhanced fuel efficiency.
- Cost-Effectiveness: The production costs of plastic molds are often lower, making them a preferred choice for high volume manufacturing.
- Complex Designs: Plastics allow for intricate designs and more detailed features that can be challenging to achieve with metal.
Key Benefits of Utilizing Automobile Plastic Mold
Utilizing automobile plastic mold technology yields numerous benefits that appeal to manufacturers aiming for excellence and innovation:
1. Enhanced Production Efficiency
One of the primary advantages of automobile plastic molds is the increased production efficiency. Plastic can be molded faster than metal, allowing manufacturers to produce more components in less time.
2. Design Flexibility
Another significant benefit is the design flexibility offered by plastic molds. The ability to create complex shapes without additional machining leads to:
- Improved Aesthetics: Manufacturers can develop visually appealing parts that enhance the overall appearance of vehicles.
- Reduced Part Count: A single molded piece can often replace multiple components, simplifying assembly processes.
3. Resistance and Durability
Modern plastics often exhibit superior resistance to environmental factors, chemicals, and wear. This durability ensures that plastic components maintain their integrity over extended periods, resulting in lower maintenance needs and longer life spans for automotive parts.
Automobile Plastic Mold Manufacturing Processes
The manufacturing processes for automobile plastic molds are varied and highly specialized. Key techniques include:
1. Injection Molding
Injection molding is the most common method used to create plastic parts for the automotive industry. This process involves:
- Heating plastic until it is pliable
- Injecting the molten plastic into the mold
- Allowing it to cool and solidify into the desired shape
This technique is valued for its efficiency and ability to produce large quantities of consistent products.
2. Blow Molding
Blow molding is another technique used primarily for hollow plastic parts. This process uses air to expand heated plastic into a mold. It’s particularly useful for:
- Fuel tanks
- Hoses
- Other hollow components
3. Thermoforming
This method involves heating a plastic sheet until it becomes malleable and then forming it over a mold. It is widely used for:
- Dashboard components
- Interior trims
- Panels
Challenges in Automobile Plastic Mold Production
While the advantages are compelling, the production of automobile plastic molds does come with its own set of challenges:
1. Material Limitations
The choice of plastic can significantly influence the properties of the finished product. Factors such as thermal stability and impact resistance play critical roles, making material selection vital.
2. Design Constraints
Although plastic offers design flexibility, there are still constraints regarding wall thickness, mold draft angles, and sink marks that must be considered during the design phase to avoid complications.
3. Sustainability Concerns
As the automobile industry shifts towards more sustainable practices, the environmental impact of plastics is under scrutiny. Efforts are being made in:
- Researching bio-based plastics
- Improving recycling methods
- Creating efficient manufacturing processes that reduce waste
The Future of Automobile Plastic Molds
The future of automobile plastic mold technology is bright, with advancements paving the way for new possibilities. Emerging trends include:
1. Advanced Materials
Research into advanced polymers promises to deliver materials that offer higher durability, lighter weight, and better integration with electric vehicles.
2. Automation and Smart Manufacturing
With the rise of Industry 4.0, the incorporation of automation and smart technologies in the molding process will enhance precision, reduce costs, and contribute to real-time monitoring and quality control.
3. Sustainable Innovations
As eco-consciousness rises, the focus will shift toward sustainable practices in production, including:
- Recyclable mold materials
- Energy-efficient production methods
- Life-cycle assessments to track environmental impact
Conclusion
In conclusion, the significance of automobile plastic mold in the modern automotive industry is profound. By enhancing production efficiency, allowing for intricate designs, and contributing to the durability of automotive parts, plastic molds are pivotal to innovation and sustainability. As we look to the future, ongoing advancements will further solidify the position of automobile plastic molds as indispensable tools within the industry. For manufacturers keen on staying ahead in this competitive landscape, investing in high-quality plastic mold technologies offered by experts like Deep Mould is crucial for success.