Exploring Lathe Machine Parts: A Comprehensive Guide
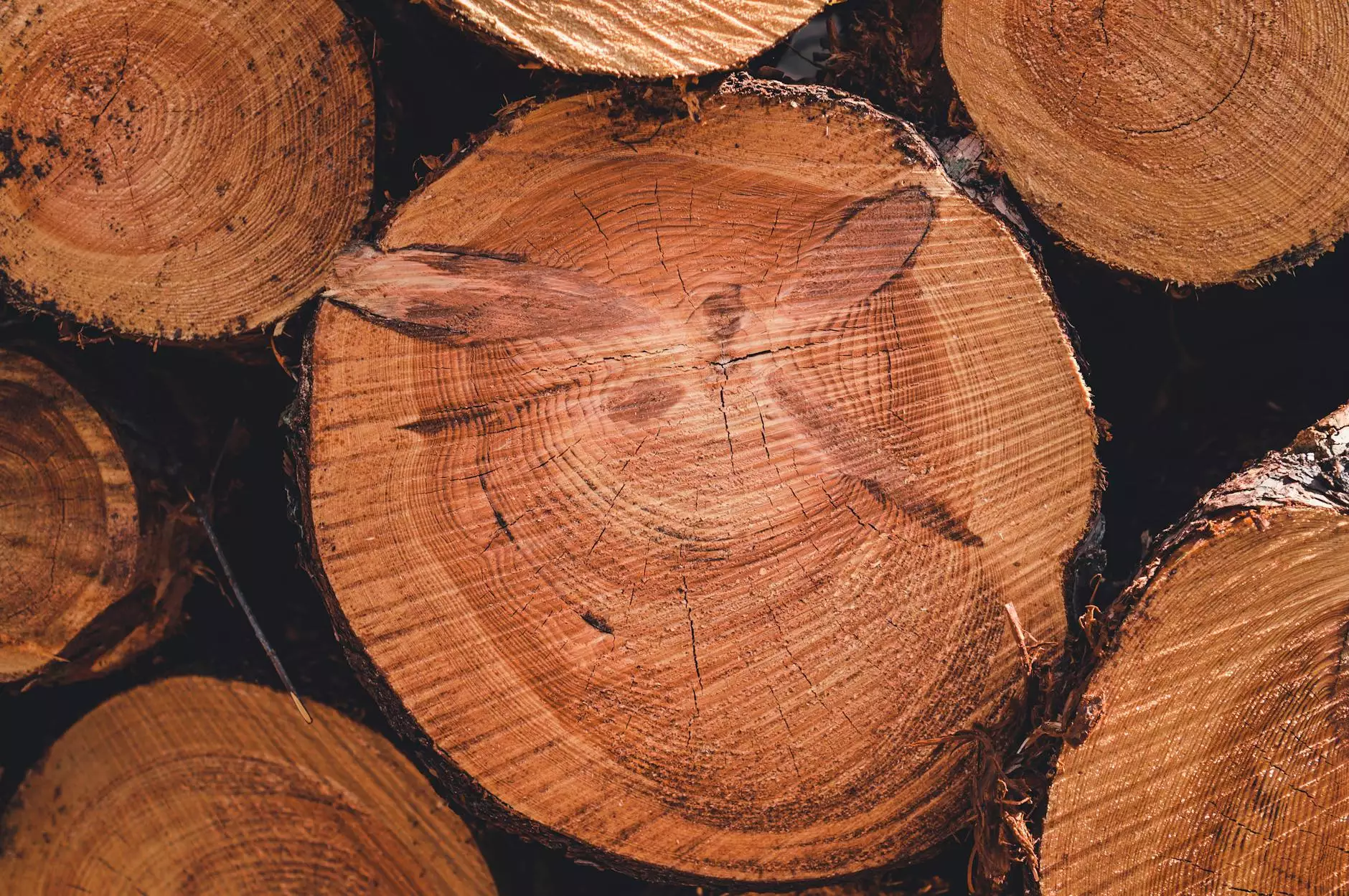
Lathe machines are pivotal in the realm of metal fabrication, delivering precision and efficiency in machining. This article delves into the intricacies of lathe machine parts, their functions, and how they contribute to the overall effectiveness of metalworking processes.
The Role of Lathe Machines in Metal Fabrication
Lathe machines are designed to shape and cut materials into desired forms. They operate by rotating the workpiece on the spindle while a cutting tool is moved along the axes. This process is vital in creating various components used in mechanical systems, automotive parts, and intricate designs in various industries.
Key Components of Lathe Machines
Understanding the main parts of a lathe machine is essential for anyone involved in metal fabrication. Below is a detailed overview of lathe machine parts:
1. Headstock
The headstock is the powerhouse of the lathe machine, housing the motor and providing the rotational force needed to spin the workpiece. It typically includes gears that allow for speed adjustments and often contains a chuck, which secures the workpiece in place.
2. Tailstock
The tailstock supports the non-driven end of the workpiece. It can be adjusted along the bed to accommodate different lengths of workpieces. Additionally, tailstocks may contain drill chucks for drilling operations.
3. Bed
The bed is the foundation of the lathe machine, providing stability and alignment for all components. It is typically made from cast iron for durability and vibration dampening, ensuring precision machining.
4. Carriage
The carriage moves along the bed and supports the cutting tool. It incorporates various mechanisms to control the movement of the tool, allowing for both longitudinal and cross-cutting operations.
5. Tool Post
The tool post is where the cutting tool is mounted. It allows for rapid tool changes and fine adjustments based on the machining needs.
6. Apron
The apron is attached to the carriage and houses controls and mechanisms for feed operations. It plays a crucial role in coordinating the movement of the cutting tool during machining.
Understanding Lathe Machine Operations
Lathe machines perform several processes, each relying on different lathe machine parts to deliver precise results. Here are some of the primary operations associated with lathe machines:
1. Turning
Turning is the process of removing material from a rotating workpiece, typically to create cylindrical shapes. This operation is fundamental in many manufacturing applications.
2. Facing
Facing involves machining the end of a workpiece to produce a flat surface. It is often the first operation performed to ensure proper alignment.
3. Boring
Boring enlarges an existing hole in a workpiece, enhancing precision for subsequent operations or assembly.
4. Threading
Threading creates helical ridges on a workpiece, allowing for the assembly of parts using screws and bolts.
5. Knurling
Knurling is a process of creating a textured pattern on a workpiece. This adds grip and enhances the aesthetic appeal of cylindrical parts.
The Importance of Quality Lathe Machine Parts
Utilizing high-quality lathe machine parts directly impacts machining performance. Below are some key reasons why quality matters:
- Precision: High-quality components ensure precise cuts and dimensions, reducing the likelihood of errors.
- Durability: Quality parts withstand wear and tear, leading to less frequent replacements and maintenance.
- Efficiency: Well-manufactured components contribute to smoother operations, enhancing overall productivity.
- Safety: Reliable parts reduce the risk of operational failures, ensuring a safer working environment.
Choosing the Right Supplier for Lathe Machine Parts
Selecting a reputable supplier for lathe machine parts is crucial for maintaining operational excellence. Here are some tips on how to choose the right supplier:
1. Experience and Reputation
Look for suppliers with a proven track record in the industry. Read reviews and testimonials to gauge their reputation among customers.
2. Quality Assurance
Ensure that the supplier adheres to stringent quality control measures. Certifications and compliance with industry standards are indicators of quality.
3. Product Range
A reliable supplier should offer a wide range of lathe machine parts to meet various machining needs. This indicates their capability and readiness to support your operations.
4. Technical Support
Technical assistance can be invaluable, especially during installation or maintenance. Ensure your supplier provides sufficient support.
5. Competitive Pricing
While quality is paramount, pricing should also be competitive. Compare quotes from multiple suppliers, but prioritize quality over cost.
Future Trends in Lathe Machine Technology
As the manufacturing sector evolves, so does the technology behind lathe machines. Staying updated on trends can help businesses remain competitive. Key trends include:
1. Automation
Automation increases efficiency and reduces labor costs. Modern lathe machines are increasingly equipped with CNC (Computer Numerical Control) technology for enhanced precision.
2. Increased Use of Materials
With advancements in materials science, new alloys and composites are becoming common in lathe machining, expanding the range of applications.
3. Smart Technology
Integration of IoT (Internet of Things) allows for real-time monitoring and predictive maintenance, improving machining processes significantly.
4. Sustainability
Modern lathe machining is focusing on sustainability, using energy-efficient technologies and reducing waste.
Conclusion
In summary, understanding the intricacies of lathe machine parts is essential in the metal fabrication industry. From the headstock to the tailstock, each component plays a crucial role in the performance and efficiency of lathe machines. Selecting high-quality parts and reliable suppliers ensures operational excellence and competitiveness in today's fast-paced manufacturing landscape.
As the industry continues to evolve, staying informed about trends and advancements will enable businesses to harness the full potential of lathe machining technology. With a firm foundation in the fundamentals of lathe machine parts, manufacturers can achieve unparalleled precision and productivity, paving the way for a successful future.